The Importance of a CNC Lathe Turning Parts Factory in Modern Manufacturing
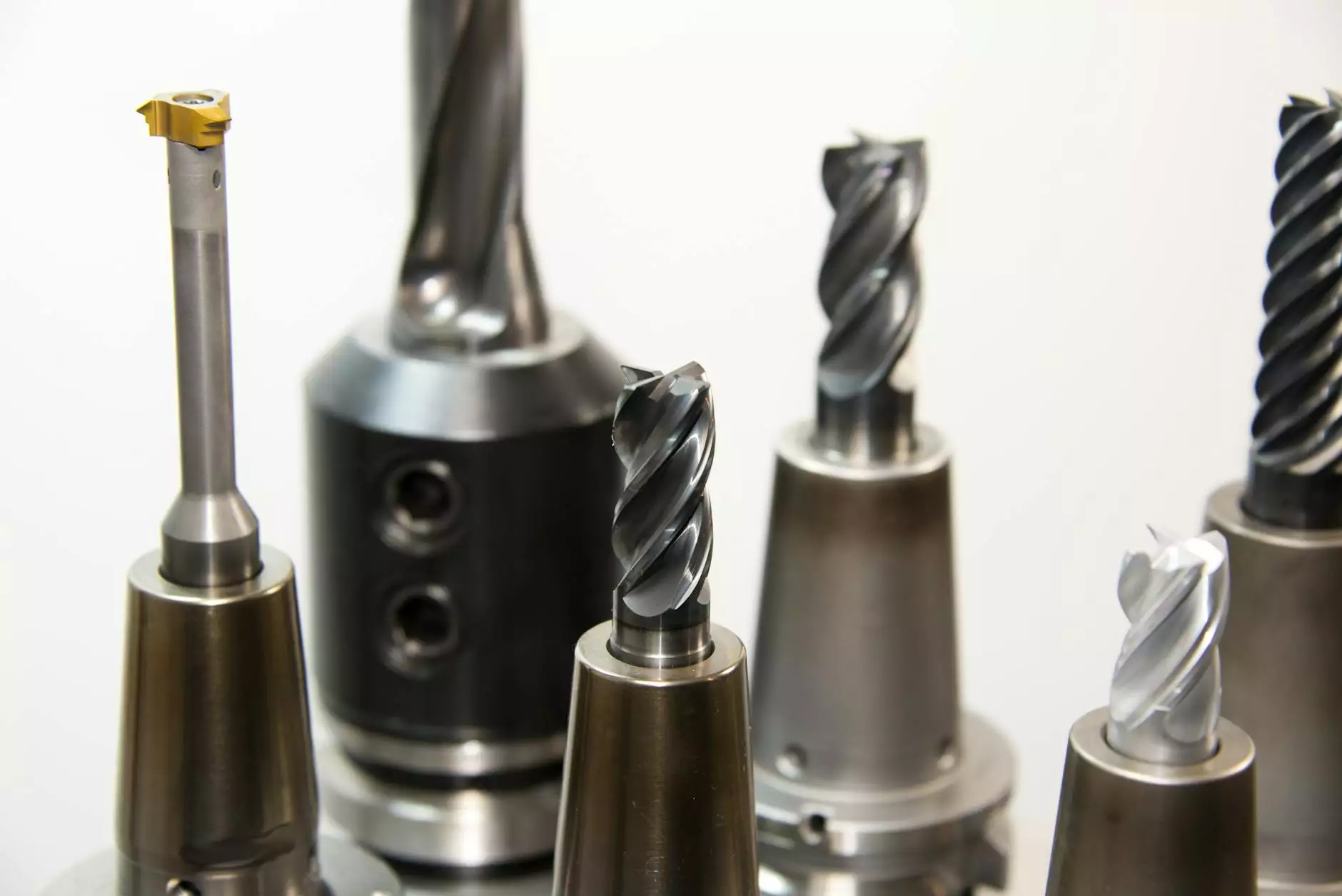
In today's fast-paced manufacturing landscape, the need for precision and efficiency has never been greater. A cnc lathe turning parts factory stands at the forefront of this evolution, leveraging advanced technologies to deliver high-quality, reliable components that drive innovation across various industries. At DeepMould.net, we understand the dynamics of metal fabrication and how CNC lathe turning processes play a crucial role in manufacturing excellence.
Understanding CNC Lathe Turning
CNC (Computer Numerical Control) lathe turning is a subtractive manufacturing process that involves shaping materials using a rotating piece of machinery. This technology allows for high accuracy, repeatability, and efficiency in producing metal components. Unlike manual lathes, CNC machines utilize computerized systems to automate movements, ensuring that each part meets precise specifications.
Key Benefits of CNC Lathe Turning
- High Precision: CNC lathes can achieve tolerances as tight as ±0.001 inches, making them ideal for industries requiring exact specifications.
- Repeatability: Once programmed, a CNC machine can produce identical parts repeatedly without variation, enhancing quality control.
- Complex Geometries: The technology allows for the creation of intricate shapes that would be challenging to produce with traditional machining methods.
- Reduced Lead Times: Automation and efficiency in CNC operations significantly cut down production times, allowing for faster turnaround on orders.
- Material Versatility: CNC lathe turning can work with various materials, including metals, plastics, and composites, making it suitable for diverse applications.
The Role of a CNC Lathe Turning Parts Factory
A cnc lathe turning parts factory is equipped with numerous CNC lathes and advanced software that control the machining process. These facilities often engage in the production of components for industries such as aerospace, automotive, medical, and electronics. Each sector has unique requirements, and a proficient factory must adapt to these demands while maintaining efficiency and quality.
1. Industry Applications of CNC Lathe Turning Parts
Understanding the industries that benefit from CNC lathe turning is essential for recognizing the technology's broad applicability:
- Aerospace: Components like shafts, brackets, and housings made with high-precision standards that meet stringent regulations.
- Automotive: Producing engine parts, transmission components, and various fittings that require durability and precision.
- Medical Devices: Manufacturing surgical instruments, prosthetics, and implants that demand both precision and biocompatibility.
- Electronics: Creating casings and connectors that require exact dimensions for functionality in devices.
2. Selecting the Right CNC Lathe Turning Parts Factory
Choosing a reliable cnc lathe turning parts factory is crucial for obtaining high-quality parts. Here are some key considerations when selecting a partner for your metal fabrication needs:
- Certification and Compliance: Ensure the factory holds relevant certifications such as ISO 9001 for quality management, which reflects their commitment to maintaining high standards.
- Technological Capabilities: Assess the types of CNC lathes they utilize—modern, high-tech machines offer better precision and efficiency.
- Experience and Reputation: Look for a factory with a strong track record in your specific industry and positive client testimonials that attest to their reliability.
- Custom Capabilities: Ensure they can handle custom orders, adapting to specific designs or changes in order quantities seamlessly.
- Customer Support: A responsive support team can make a difference during the design phase and throughout the production process.
Quality Control in CNC Lathe Turning Parts Manufacturing
Quality control is paramount in the manufacturing of CNC lathe turning parts. At a reputable cnc lathe turning parts factory like DeepMould.net, quality assurance involves systematic tracking of the production process through several stages, ensuring that each component meets or exceeds industry standards.
Quality Control Measures
- Inspection: Parts are inspected at various stages using advanced measuring tools like CMM (Coordinate Measuring Machines) and calipers.
- Testing: Functional and stress tests are conducted to ensure that components can withstand the conditions they will face in real-world applications.
- Documentation: Keeping detailed records of each batch produced, including dimensions and any tests performed, is crucial for traceability.
- Feedback Loops: Continuous improvement processes are in place, where data from previous productions are analyzed to enhance future outputs.
Cost-Efficiency of CNC Lathe Turning Parts
While initial investments in CNC lathe technologies can be significant, the long-term savings and cost-efficiency realized through precision manufacturing outweigh the initial costs. The advantages include:
- Reduced Waste: CNC lathes optimize material use, leading to less scrap compared to traditional machining methods.
- Labor Savings: Automation minimizes labor costs, requiring fewer operators while maintaining high production rates.
- Minimized Rework: High precision reduces the likelihood of errors and the need for rework, which can eat into profit margins.
- Scalability: As demand increases, CNC machines can adapt to larger quantities without a significant increase in unit costs.
Future Trends in CNC Lathe Turning
The future of CNC lathe turning is poised for exciting advancements. Here are some trends that are likely to shape the industry:
- Integration of AI and Machine Learning: Factories are beginning to utilize AI to predict machine maintenance and optimize production schedules.
- Increased Automation: Fully automated factories with less human intervention are becoming a reality, enhancing efficiency further.
- Sustainability Initiatives: More factories are adopting eco-friendly practices, such as recyclable materials and energy-efficient machines.
- Advanced Materials: New alloys and composites are being developed, requiring CNC technology to adapt to new fabrication challenges.
Conclusion
The role of a cnc lathe turning parts factory cannot be overstated in today's manufacturing. With cutting-edge technology, stringent quality control, and capabilities to meet diverse industry demands, factories like DeepMould.net excel in providing precision machined components crucial for various applications. When selecting a partner for your manufacturing needs, consider their technological capabilities, quality assurance processes, and commitment to meeting your unique specifications, ensuring you remain competitive in your field.
Investing in a reputable CNC lathe turning parts factory will help you elevate your product quality while reducing overall costs, making it a worthwhile endeavor for manufacturers seeking long-term success in a competitive market.