The Importance of Prototype Molds in Modern Manufacturing
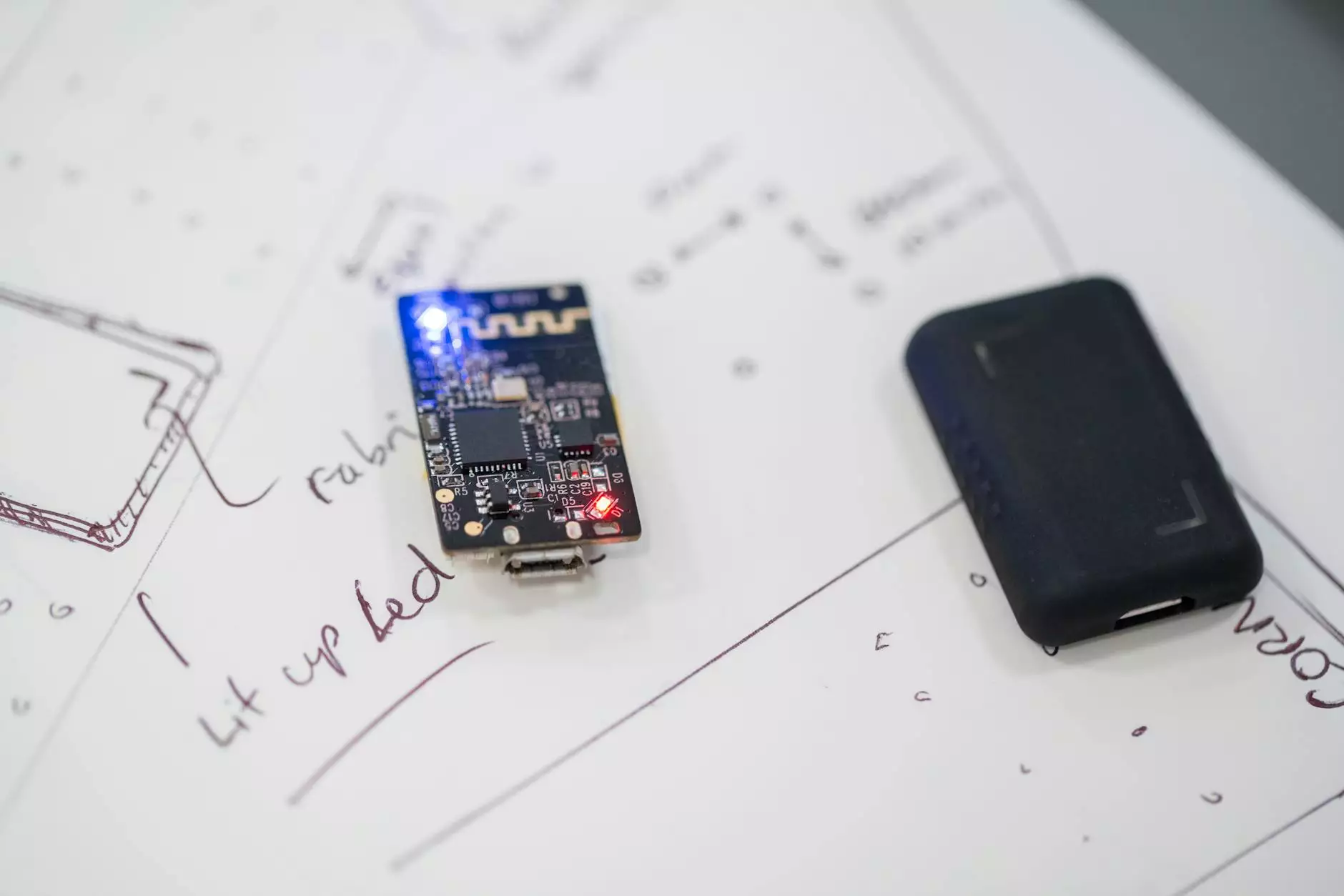
In today's fast-paced manufacturing environment, prototype molds are essential tools that bridge the gap between conceptual designs and the production of tangible products. They serve as the first step in bringing creative ideas to life, allowing manufacturers to test and refine their concepts before full-scale production. This article will delve deep into the world of prototype molds, explaining their roles, benefits, applications, and how they are transforming the manufacturing landscape.
What are Prototype Molds?
A prototype mold is a specialized tool used to create plastic parts or components in the early stages of product development. These molds are often employed in various manufacturing processes, including injection molding and blow molding. By utilizing prototype molds, manufacturers can create single parts or small batches of products to assess their design, functionality, and feasibility.
Benefits of Using Prototype Molds
- Cost-Effective Testing: Prototype molds significantly reduce costs associated with product development. By allowing manufacturers to test designs before committing to mass production, they avoid costly mistakes.
- Time Efficiency: Rapid prototyping enables developers to bring their concepts to market faster. Quick iterations enhance the design process, ensuring expedited feedback and revisions.
- Design Validation: Early-stage feedback from prototype molds helps validate product designs, ensuring that the final product meets both functional and aesthetic requirements.
- Material Selection: Prototype molds help manufacturers experiment with different materials, allowing them to determine the best fit for the product in terms of performance and durability.
The Prototype Mold Development Process
The process of creating a prototype mold involves several steps, each critical to ensuring that the final product meets desired specifications. This process typically includes:
1. Conceptualization and Design
Developing a prototype mold begins with conceptualizing the product design. Designers use CAD (Computer-Aided Design) software to create detailed blueprints, incorporating all necessary specifications and features.
2. Selecting Materials
Choosing the right material for the mold is crucial. Materials like aluminum and steel are commonly used due to their durability and ability to withstand repeated use. The choice depends on various factors, including the anticipated volume of production and the complexity of the design.
3. Fabrication of the Mold
Once the design is finalized and materials selected, the mold is fabricated using advanced techniques such as CNC machining. This step requires precision to ensure that the mold accurately reflects the intended design.
4. Testing and Iteration
After fabrication, the mold undergoes rigorous testing. Various prototypes are produced to assess functionality and design flaws. Feedback from these tests leads to necessary modifications, ensuring that the final mold is production-ready.
Applications of Prototype Molds
Prototype molds find applications across multiple industries, each benefiting from their unique advantages. Some key sectors that utilize prototype molds include:
1. Automotive Industry
The automotive sector relies heavily on prototype molds for creating complex parts and components. Manufacturers can quickly produce and test various designs for dashboards, levers, and other critical elements before mass production, ensuring compliance with safety standards and performance metrics.
2. Consumer Electronics
For consumer electronics, prototypes are crucial in refining product designs. Companies can assess ergonomics and technical functionalities of devices like smartphones and tablets, making necessary adjustments based on prototype testing.
3. Medical Devices
In the medical field, precision is paramount. Prototype molds allow for the development of intricate medical devices and components, facilitating compliance with regulatory requirements while ensuring functionality and safety.
4. Aerospace
Aerospace manufacturers utilize prototype molds to produce lightweight yet durable components that adhere to strict performance and safety regulations. The rapid prototyping process allows for innovations that keep pace with technological advancements.
Choosing the Right Prototype Mold Manufacturer
- Experience and Expertise: Look for manufacturers with a proven track record in creating prototype molds for your specific industry.
- Technological Capabilities: Ensure that the manufacturer utilizes advanced machinery and technology in the mold-making process to achieve precision and accuracy.
- Material Knowledge: A good manufacturer should guide you in selecting the best materials for your prototype molds, considering the intended use and production volumes.
- Customer Support: Reputable manufacturers offer robust customer support throughout the development process, addressing concerns and providing updates on progress.
The Future of Prototype Molds
The world of manufacturing is constantly evolving, and prototype molds are at the forefront of several exciting developments:
1. 3D Printing and Additive Manufacturing
With advancements in 3D printing technology, prototype molds are becoming more versatile and accessible. Additive manufacturing allows for rapid prototyping and complex geometries that traditional methods may struggle to achieve.
2. Increased Customization
As consumer demand for customized products rises, prototype molds will play a pivotal role in facilitating personalization in manufacturing. Companies that can quickly produce prototype molds will have a competitive edge.
3. Sustainability Initiatives
The manufacturing industry is shifting towards more sustainable practices. Prototype molds can be developed using eco-friendly materials and processes, reflecting a company's commitment to environmental responsibility.
Conclusion
The role of prototype molds in modern manufacturing cannot be overstated. They are essential for validating designs, reducing costs, and accelerating product development processes. In an environment where time to market is critical, investing in high-quality prototype molds is vital for any manufacturer aiming to stay competitive. As technology continues to evolve, those who embrace innovative practices in mold-making will lead the charge towards more efficient and customizable production methods.
For those looking to enhance their product development processes, consider collaborating with a trusted manufacturer of prototype molds, such as DeepMould.net, where expertise in metal fabrication meets a commitment to quality and innovation.