Lift Station Monitoring with Cloud SCADA: Optimize Your Business Operations
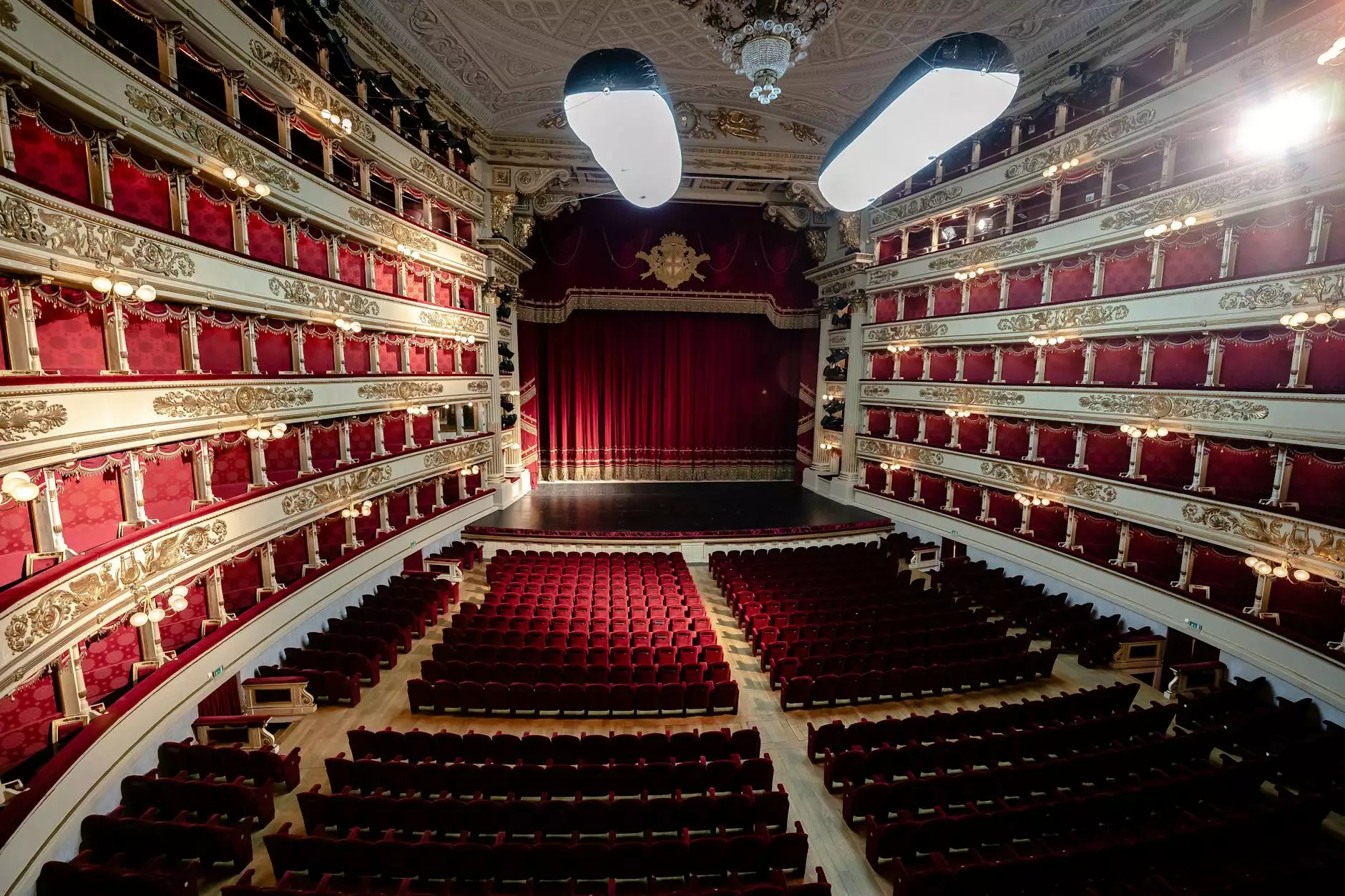
The landscape of industrial operations is evolving, with technology leading the charge towards enhanced efficiencies and better resource management. A significant aspect of this transformation is the adoption of Cloud SCADA (Supervisory Control and Data Acquisition) systems, particularly in lift station monitoring. With growing concerns regarding safety equipment and auto parts & supplies, businesses must leverage innovative solutions to remain competitive.
Understanding Lift Station Monitoring
Before diving into the specifics of lift station monitoring cloud SCADA, it's essential to understand what lift stations are and their role in various business sectors.
What is a Lift Station?
A lift station is a crucial component in wastewater and stormwater management, designed to move sewage and water from lower to higher elevations. They play an integral role in municipal water systems, drainage systems, and even in industrial applications. Ensuring these systems operate smoothly is critical for overall efficiency and safety.
Cloud SCADA: The Future of Monitoring
Cloud SCADA refers to a modern approach that leverages cloud computing technology to enhance supervisory control systems. This system allows for remote monitoring and control of critical processes, making it an indispensable tool for modern industry operations.
Key Benefits of Cloud SCADA in Lift Station Monitoring
- Real-time Data Access: Cloud SCADA provides operators with instant access to real-time data. This transparency enables swift decision-making based on current operational statuses.
- Scalability: Businesses can easily scale their monitoring solutions as their operations grow without the need for extensive physical infrastructure.
- Cost-Effectiveness: Reducing the need for on-site hardware can lead to significant cost savings. Cloud solutions often operate on a subscription model, minimizing upfront investments.
- Enhanced Reliability: Cloud providers typically offer robust redundancies and backups, ensuring data integrity and availability even during outages.
- Improved Collaboration: With data accessible anywhere, team members can collaborate more effectively, regardless of their physical location.
The Role of Lift Station Monitoring in Safety Equipment and Auto Parts
For businesses operating in sectors related to safety equipment and auto parts, implementing an efficient monitoring system through cloud SCADA is essential. Here’s how it benefits these domains:
Enhancing Safety Equipment Reliability
Lift stations often use various safety equipment to operation effectively. By monitoring these systems via cloud SCADA, businesses can ensure:
- Immediate Alerts: Detecting potential failures in safety equipment promptly.
- Predictive Maintenance: Utilizing data analytics to predict when maintenance is necessary, reducing unexpected downtimes.
- Compliance Assurance: Maintaining records that demonstrate regulatory compliance for safety standards.
Optimizing Auto Parts Supply Chains
*Cloud SCADA* can also streamline operations related to auto parts & supplies. Here’s how:
- Inventory Management: Real-time tracking of parts used and needed, reducing excess inventory and improving cash flow.
- Enhanced Scheduling: Coordinating with suppliers for timely deliveries based on current operational demands.
- Data Analytics: Leveraging data insights to improve forecasting and demand planning.
Best Practices for Implementing Lift Station Monitoring with Cloud SCADA
Implementing lift station monitoring cloud SCADA requires a strategic approach. Here are some best practices to ensure success:
1. Define Clear Objectives
Before integrating a cloud SCADA system, businesses must identify their specific goals. Whether it’s cost reduction, improved efficiency, or enhanced safety, clear objectives will guide the entire process.
2. Select the Right Provider
Choosing a cloud SCADA provider is crucial. Look for a vendor that offers robust security features, excellent customer support, and a proven track record in your industry.
3. Invest in Training
Ensure that your team is adequately trained to utilize the new system effectively. An investment in training will lead to better adoption and more efficient use of resources.
4. Regularly Review and Optimize
After implementation, regularly review the system's performance against your defined objectives. Use this data to make necessary optimizations for even better results.
Challenges in Cloud SCADA Implementation
While the benefits of lift station monitoring cloud SCADA are significant, there are challenges to be aware of:
Data Security Concerns
As with any cloud-based system, data security is paramount. It’s essential to ensure that the provider has robust security measures to protect sensitive information.
Integration with Legacy Systems
Many businesses operate legacy systems that may not easily integrate with modern SCADA solutions. Consideration of interoperability is crucial during the planning phase.
Initial Investment
Even though cloud solutions can be cost-effective in the long run, initial investments in software and training can pose a challenge for some businesses.
Conclusion
Adopting lift station monitoring cloud SCADA represents a significant leap forward for businesses in safety equipment and auto parts sectors. The benefits of real-time monitoring, enhanced safety, and improved operational efficiencies are compelling reasons for making this transition. Despite the challenges, the long-term advantages of integrating advanced technology into lift station operations pave the way for sustainable growth and improved service delivery.
For businesses aiming to enhance their operational capabilities through revolutionary technology, embracing lift station monitoring with cloud SCADA is not just an option—it's a necessity. As industries continue to evolve, staying ahead of the curve will enable organizations to maintain competitive advantage and ensure long-term success.