Understanding Titanium Screw Manufacturers: A Comprehensive Guide
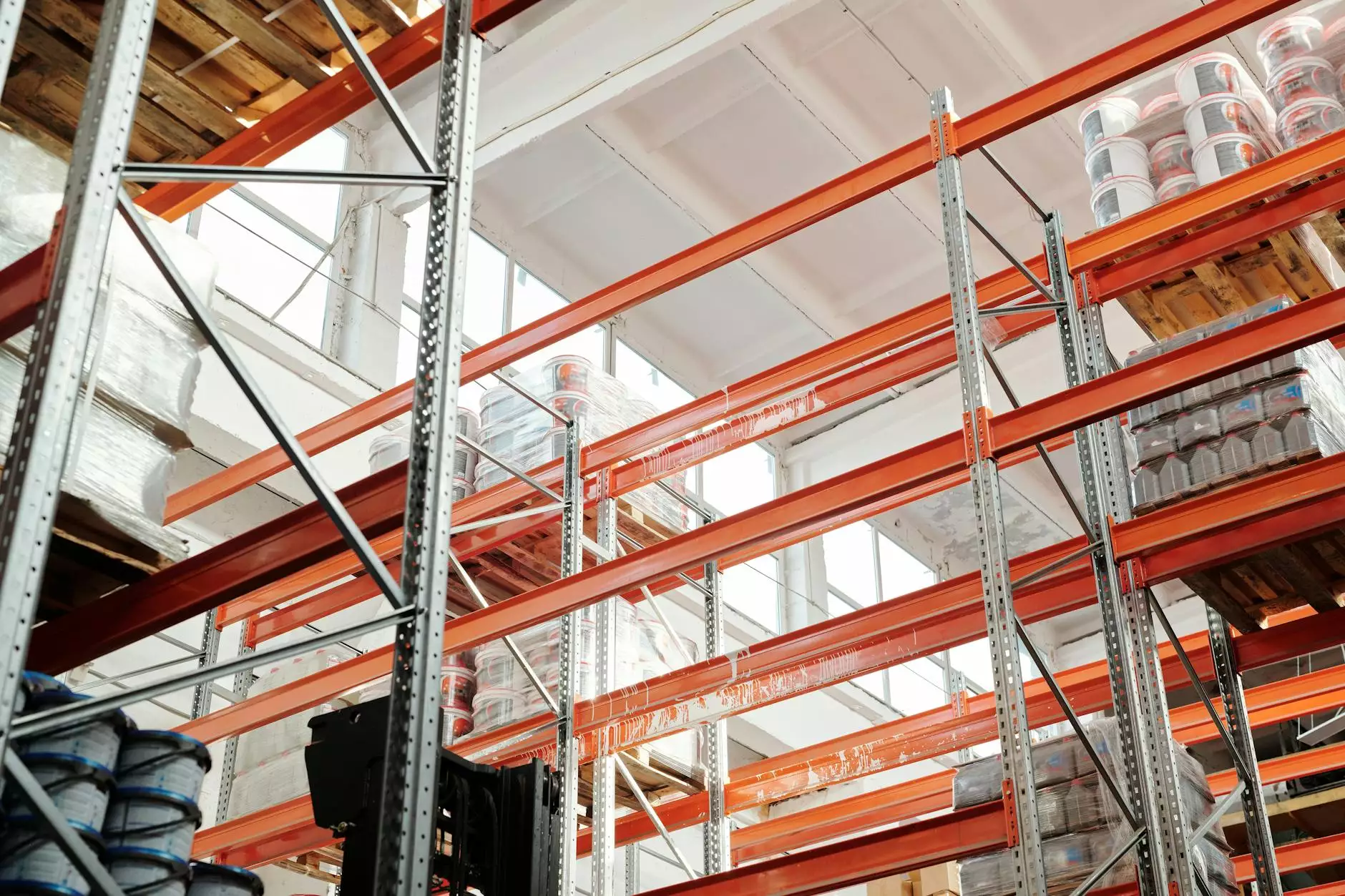
Titanium is a remarkable metal that has captured the interest of industries across the globe. Its strength, lightweight nature, and corrosion resistance make it a preferred choice for several applications, particularly in the production of screws. In this article, we delve into the world of titanium screw manufacturers, exploring their significance, the properties of titanium, and the manufacturing processes involved.
The Significance of Titanium Screws in Modern Industries
Titanium screws are integral components in numerous industries including aerospace, automotive, medical, and marine. The following points highlight their importance:
- Strength-to-Weight Ratio: Titanium boasts a high strength-to-weight ratio, making it ideal for applications where minimizing weight is crucial.
- Corrosion Resistance: Unlike steel, titanium does not rust or corrode easily, which ensures longevity in adverse environments.
- Biocompatibility: In the medical field, titanium’s biocompatibility allows it to be used in implants and surgical devices without causing adverse reactions.
- Heat Resistance: Titanium can withstand high temperatures, making it perfect for aerospace applications.
What Sets Titanium Apart from Other Metals
Titanium is often compared with other metals, such as steel and aluminum. Here are some distinct advantages of titanium:
- Lower Density: Titanium is less dense than steel yet stronger, which provides an advantage in weight-sensitive designs.
- Superior Fatigue Resistance: Titanium has a higher resistance to fatigue, prolonging the lifespan of screws used in dynamic applications.
- Non-Magnetic Properties: Titanium is non-magnetic, which is essential for many electronic and medical applications.
How Titanium Screws are Manufactured
The manufacturing process of titanium screws involves several critical steps. Understanding these steps reveals the complexity and precision necessary to produce high-quality fasteners.
1. Material Selection
The first step in manufacturing titanium screws is selecting the right grade of titanium. There are several grades available, and each has specific properties suited for different applications. The most commonly used grades for screws include:
- Grade 2: Often referred to as the workhorse of titanium, it has excellent corrosion resistance and formability, making it suitable for various applications.
- Grade 5 (Ti-6Al-4V): This is an alloy with aluminum and vanadium that offers increased strength and is widely used in aerospace applications.
- Grade 23: A higher standard of Grade 5 with improved mechanical properties and exceptional biocompatibility, often used in medical implants.
2. Forming Techniques
Once the material is selected, various forming techniques can be employed to create titanium screws, including:
- Cold Heading: This method involves deforming the titanium at room temperature to create the head of the screw. It enhances mechanical properties due to strain hardening.
- Machining: Portions of the screw can be machined to achieve precise dimensions and threads.
- Thread Rolling: Instead of cutting the threads, this method forms them by displacing material, which can increase the strength of the threads.
3. Heat Treatment
After forming, titanium screws often undergo heat treatment to improve their mechanical properties. Processes like annealing help relieve stresses induced during forming and maintain the desired hardness and strength.
4. Surface Finishing
To enhance corrosion resistance and aesthetic appeal, screws may undergo surface treatments such as anodizing, coating, or polishing. These treatments can also improve wear resistance.
5. Quality Control
Quality control is paramount in the manufacturing process of titanium screws. Rigorous testing for strength, fatigue resistance, and corrosion resistance must be performed to ensure compliance with industry standards.
Applications of Titanium Screws
Titanium screws have found a niche in several sectors due to their superior properties. Here’s a look at their primary applications:
Aerospace Industry
The aerospace sector demands fasteners that can withstand extreme conditions. Titanium screws are essential in aircraft construction due to their lightweight and strength, contributing to fuel efficiency and performance.
Medical Implants
In the medical field, titanium screws are used in orthopedic implants, dental applications, and surgical devices because they are non-toxic and biocompatible.
Automotive Industry
As the automotive industry leans towards lighter materials for better fuel economy, titanium screws are increasingly being utilized in high-performance cars and racing vehicles.
Marine Applications
Given their corrosion resistance, titanium screws are employed in marine environments for boatbuilding and underwater construction, ensuring durability and longevity.
The Future of Titanium Screws
The demand for titanium screws is projected to grow, driven by advancements in technologies and the increasing acceptance of titanium in various industries. Here are some trends that may shape the future:
- 3D Printing: The rise of additive manufacturing is likely to innovate the production process of titanium screws, making them more customizable and cost-effective.
- Research and Development: Ongoing R&D efforts aim to produce new titanium alloys that can meet specific industry demands, enhancing performance and reducing costs.
- Sustainability: As industries move towards more sustainable practices, using titanium can reduce the carbon footprint due to its recycling capability.
The Role of Titanium Screw Manufacturers
Titanium screw manufacturers play a vital role in ensuring that industries have access to high-quality fasteners. Companies like TitaniumBolts.com are at the forefront, providing a range of products and solutions tailored to meet diverse industry needs.
Choosing the Right Manufacturer
Selecting a trustworthy manufacturer involves several considerations:
- Certifications: Ensure the manufacturer complies with industry standards and has the necessary certifications for quality assurance.
- Customization Options: Look for manufacturers that offer customization to meet specific project requirements.
- Experience and Reputation: A manufacturer with a solid reputation and extensive experience in titanium screw production often assures quality and reliability.
Conclusion
In the fast-evolving world of technology and materials science, titanium screw manufacturers are critical in supplying high-quality fastening solutions that meet the rigorous demands of various industries. With its unique properties such as strength, corrosive resistance, and lightweight, titanium is poised to continue its growth in demand across multiple sectors. As advancements in manufacturing techniques and materials develop, the future looks bright for titanium screws, foreseeing greater innovation and application in the years to come.